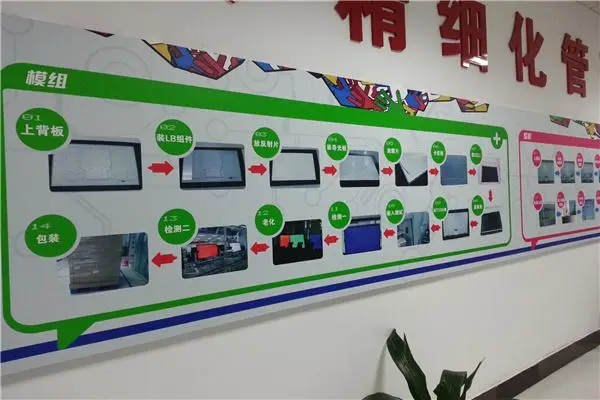
Company News
Freshness Keeper Formulate Regulation of Molding Injection Workshop
Freshness Keeper in order to standardize the working order of food container production workshop, improve working environment, improve production efficiency, this regulation is specially formulated:
Part 1: 5S field management
5S: Seiri, Seito, Seiso, Seikeetsu, Shitsuke
Specific requirements are as follows:
1. Work 10 minutes in advance for each shift to prepare for production. Such as inspection of food containers production raw materials, operating tools, cartons, product labels, etc.
2. Clear all the items that are not relevant to the current work and put them in the corresponding position specified;
3. The food containers, semi-finished products and finished products made by each class must be placed in the designated area and clearly marked;
4. Tie up loose ends at the end of the day. Every shift must do a good job of site cleaning and machine cleaning. The waste materials of each shift should be placed in the designated position in time and clearly marked. The waste should be dumped at the end of the night shift.
5. All kinds of articles are not allowed to be placed in an orderly manner. The items taken out must be promptly returned and neatly placed when not in use;
6. After changing the mold or adjusting the machine, the machine and the tools on the site must be cleaned in time, and the operators should clean the site. Do not start the machine if it is not clean;
7. Smoking and eating snacks during working hours are strictly prohibited in the injection molding workshop!
8. Keep the site clean and supervise each other!
Part 2: On-site work
1. Employees must fill in the daily report timely and truthfully, and have it signed by the shift supervisor for confirmation;
2. If there is any interruption in the production process, such as machine repair, machine adjustment, mold change, refueling and other work, the occurrence time, what happened and the time used should be written on the daily report, and the processing personnel should sign for confirmation;
3. Do a good job of transition. Such as the operation of the machine, the production of food containers and matters needing attention in the production process should be explained to the succession personnel;
4. In the process of production, if there are all kinds of emergencies, such as changes in product quality, machine abnormalities, etc., the operator cannot solve by himself, must timely report to the relevant supervisor, and assist them to solve;
5. Before starting the machine, it is necessary to confirm the food containers, raw materials and process parameters to be produced. Only after all process parameters meet the requirements can the machine be started;
6. It is strictly prohibited to change the process parameters arbitrarily;
7. Strictly comply with quality standards and make relevant records.
If a large number of food containers are discarded or reworked after storage or delivery, which is caused by negligence or mistake of the operators, all the consequences shall be borne by the operators on duty, quality inspection, foreman, supervisor, etc. The rework shall be completed by the direct operator outside the normal working hours, and the overtime pay shall not be calculated, and the loss shall be compensated as appropriate!
8.It is strictly prohibited to waste raw materials and do any harm to the machinery, equipment, mold, product quality and other harm to the interests of the company! Once found, a heavy fine shall be imposed; Serious cases to be removed from the list!
Part 3: Responsibilities of workshop personnel
1. Operators:
(1) Operate the machine correctly according to the operating rules to make qualified food container products;
(2) When quality problems occur, the process parameters should be reasonably adjusted according to the process debugging guidance; If unable to solve the problem by itself, report to the relevant supervisor in time;
(3) At the beginning of each batch production, take the initiative to deliver the first piece to the quality inspection personnel. The specific number of pieces shall be determined by the quality inspection personnel, and the normal production can only be carried out after the confirmation of the quality inspection personnel.
(4) Do a good job of product self-inspection, any emergency situation can not be solved by themselves must be timely to the shift supervisor report;
(5) Feeding work in the production process of each shift;
(6) Do a good job of shift handover. If the shift staff fails to finish the work, the replacement staff may refuse to take over the shift and report to the shift supervisor in time. If the work is delayed due to this situation, all the consequences shall be borne by the personnel on duty.
(7) Do the site and machine cleaning work, strictly prohibit waste of raw materials, and mutual supervision!
2. Auxiliary personnel:
(1) Be responsible for the removal of raw materials, the crushing and batching of return materials and the feeding work in the plastic food containers production process;
(2) All kinds of consumable products (such as release agent, rust inhibitor, etc.) take out and recover, do the 5S management work on the site, keep the site clean;
(3) Assist operators in cleaning and packaging products;
(4) When necessary, replace the operator to operate the machine!
The above regulations will be implemented from the date of issuance. Please cooperate actively and make joint efforts to create a good working environment with high efficiency!
Post time: Dec-13-2022